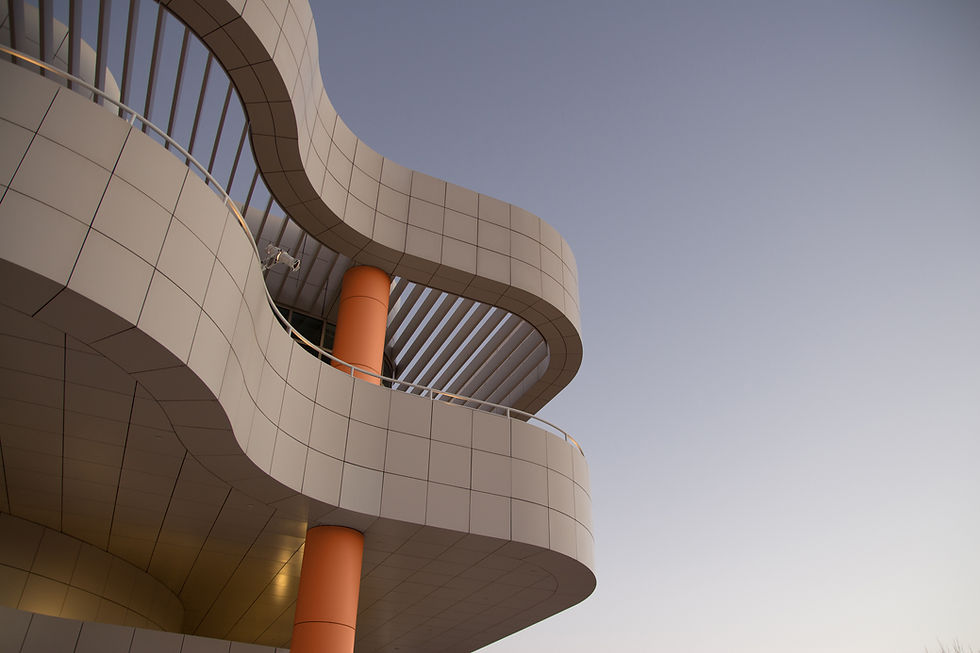
Discover the detailed steps involved in the manufacturing process of high-pressure hydraulic hoses.

A hydraulic hose is a flexible, high-pressure tube used to transport hydraulic fluid between various hydraulic components, such as valves, tools, and actuators, essential for powering and controlling hydraulic machinery in industrial and mobile applications. Hydraulic hoses are applicable in industries such as construction, agriculture, mining, manufacturing, transportation, marine, oil and gas, aerospace, forestry, and waste management. It is necessary to build good quality hydraulic hoses to ensure reliable performance, prevent system failures, enhance safety, and extend the lifespan of hydraulic systems in demanding industrial applications. Some of the top hose manufacturers in the UK include Parker Hannafin, Gates and Manuli Hydraulics.
How to make hydraulic hoses in 6 steps:
1. Selecting the Right Materials
Â
The first step in making hydraulic hoses is selecting the right materials. The materials used for hydraulic hoses must be able to withstand high pressure and extreme temperatures. Common materials include synthetic rubber, thermoplastics, high-tensile steel wire, fluoropolymers, silicone, elastomers, and thermoplastics to name a few. The choice of material is decided by the application and the needs of the hydraulic system.
Â
2. Prepping the Materials (rubber liner and high-tensile braid)
Initiating the manufacturing of hydraulic hoses requires meticulous preparation of raw materials to ensure seamless production. Sourcing and readying a sufficient quantity of raw materials is crucial to create the specific hose type needed. This phase is essential for ensuring quality and durability.
Utilizing rubber mixing machines is a key process in hydraulic hose manufacturing. These machines blend essential raw materials to create the inner liner of the hose. The inner liner directly impacts hose performance and longevity, requiring careful mixing for properties like flexibility, strength, and resistance.
This meticulous material preparation ensures high-quality hydraulic hoses that meet industry standards and customer expectations.
Â
3. Extruding the rubber to create the inner liner
Rubber extruding machines play a crucial role in the initial stage of hydraulic hose production. These machines are designed to forcefully push rubber material through a specifically shaped die to form a continuous, uniform inner liner of the hose.
During this process, a steel rod is strategically placed within the extruder. This rod serves a dual purpose: it helps shape the rubber into a tubular form and ensures that the inner diameter of the resulting hydraulic hose is consistent and precise.
The diameter of this steel rod is a critical factor as it directly determines the inner diameter of the finished hose, which is a key specification for ensuring the hose fits correctly with hydraulic system components and functions efficiently under various pressures and conditions.
4. Braiding and Reinforcement
The next step in the manufacturing process is braiding and reinforcement. This is what gives hydraulic hoses their strength and ability to withstand high pressure. The reinforcement layer is typically made of high-strength materials such as steel wire or synthetic fibres.
The reinforcement layer is applied to the inner tube of the hose, which provides the hydraulic functionality. The braiding process involves weaving the reinforcement material in a specific pattern to ensure maximum strength and flexibility.
For hoses that require multiple layers of reinforcement, each layer is added sequentially.
Braided – A braiding machine equipped with multiple bobbins is utilised to form a criss-cross braided reinforcement for braided hydraulic hoses.
Spiral – Spiral hydraulic hoses require a distinct process and machine, as indicated by their name, with the braid wrapped in a spiral around the inner liner. Typically, spiral hoses operate at a higher pressure than steel braided hoses.
Textile - Hydraulic hoses reinforced with textile use high-strength fabrics like polyester or aramid instead of steel wire. These hoses are typically employed for low- to medium-pressure applications, providing flexibility, a lightweight design, and excellent abrasion resistance.
The textile reinforcement can be arranged in braided or spiral layers, based on the needed strength and flexibility. They are frequently utilised in industrial machinery, return lines, and suction applications where metal reinforcement is not required.
5. Covering and Curing
After the braiding and reinforcement process, the hoses are covered with a protective layer. This layer serves to protect the reinforcement and inner tube from external damage such as abrasion, chemicals, and UV exposure.
The covering material can be made of rubber or thermoplastic, depending on the specific requirements. It is applied to the hose using a process called extrusion or wrapping. The covering layer is then cured, either through heat or chemical processes, to ensure it adheres to the hose and forms a strong bond.
Â
The curing process also helps to enhance the overall durability and resistance of the hose against various environmental factors.
Â
6. Quality Control and Testing
The final but most important step in the manufacturing process of hydraulic hoses is quality control and testing. This is crucial to ensure that the hydraulic hoses meet the required specifications and standards.
Various tests are performed to check the integrity, functionality, and performance of the hoses. These tests may include pressure testing, leak testing, temperature testing, and flexibility testing.
Additionally, visual inspections are carried out to check for any defects or irregularities in the hoses. Any non-conforming hoses are rejected and not shipped to customers.
By conducting rigorous quality control and testing, manufacturers can guarantee the reliability and safety of their hydraulic hoses.
If you are facing technical or quality challenges with your current supply, or looking for a reliable hose assembly, get in touch with craig.thomas@lister.co.uk. Lister Fluid Power is a leading supplier of hydraulic hose, fittings, adaptors and ancillary components from globally recognised brands like Parker Hannafin, Gates and Manuli Hydraulics.
Written By Craig Thomas
Craig Thomas brings over 30 years of expertise in fluid power solutions and heads the fluid power division at James Lister and Sons Co., based in Sandwell Industrial Estate, England. When he’s not busy working on product innovation, Craig shares his knowledge about the fluid power industry through blogs and LinkedIn. Connect with Craig today!